- HomePage /
- Sector News /
- Industry 4.0 /
- INDUSTRY 4.0 AND MAINTENANCE
INDUSTRY 4.0 AND MAINTENANCE
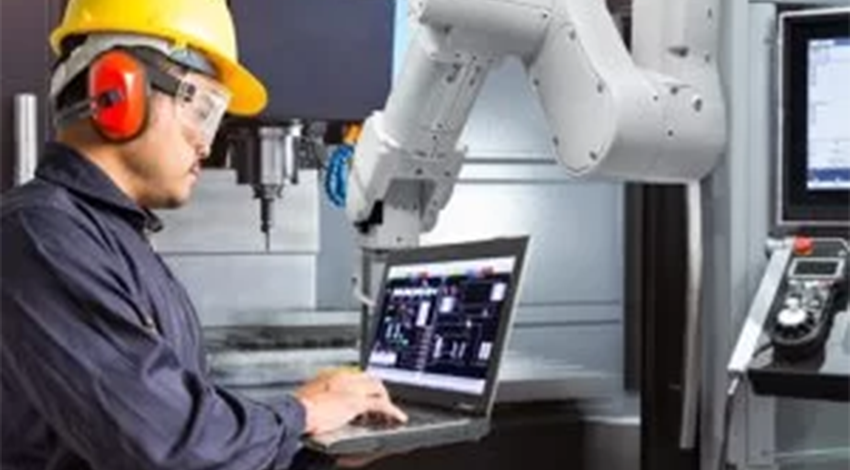
Predictive Maintenance: A Key Component of Industry 4.0
Predictive maintenance is one of the crucial applications in the realm of Industry 4.0, leveraging real-time data and advanced analytics to monitor machine health and prevent failures before they occur. By analyzing various parameters such as vibration, temperature, humidity, metal particles in machine oil, pressure, noise, and electrical current values, predictive maintenance helps identify potential issues within machines.
Key Benefits of Predictive Maintenance:
- Continuous Monitoring: Machines are continuously monitored for signs of wear or malfunction, allowing for proactive maintenance.
- Predictive Maintenance: Maintenance is scheduled based on data-driven insights rather than on fixed intervals or reactive measures.
- Reduction in Spare Parts Inventory Costs: Accurate predictions allow for a reduction in the need for spare parts inventory.
- Data-Driven Decision Making: Maintenance and operational decisions are based on actual data, minimizing subjective judgments.
- Sensor-Driven Insights: Sensors collect and transmit critical maintenance, production, and quality information to ensure operational efficiency.
- Reduced Downtime: By addressing potential issues before they result in breakdowns, predictive maintenance reduces unplanned downtimes.
- Prevention of Stock Between Machines or Processes: Better maintenance practices help reduce unnecessary inventory between production stages.
- Increased Efficiency: Optimizes the efficiency of machinery, materials, and human resources.
- Flexibility: Allows for short production runs with minimal downtime, improving responsiveness to changes in demand.
- Universal Data Collection System: A centralized data system that works across different machine and system manufacturers, improving integration and coherence in maintenance efforts.
Predictive Maintenance Process:
-
Data Collection: Sensors installed on machines or mobile sensors attached to devices collect various operational parameters. These sensors send data to the central data collection unit via WiFi, ensuring constant monitoring while the facility is in operation.
-
Remote Monitoring: The collected data is remotely monitored, ensuring that it remains within predefined control limits (upper and lower bounds). If the data deviates from these limits, it triggers further investigation.
-
Data Analysis and Recalculation of Limits: As data accumulates, new action trigger limits and control thresholds are recalculated. This continuous learning improves the accuracy of predictive models over time.
-
Alert and Action: When data approaches action trigger limits, relevant personnel receive notifications (e.g., on tablets). This allows them to plan maintenance ahead of time, minimizing disruptions to production schedules.
-
Maintenance Scheduling: The maintenance process is planned according to the urgency and required parts, ensuring that downtime is kept to a minimum. Once parts are acquired, maintenance can proceed without negatively impacting production.
-
Equipment Upgrades: In order to implement predictive maintenance, companies must update or upgrade their equipment to integrate sensors and data transmission systems. This step ensures that the equipment is capable of providing the necessary data for predictive analytics.
Summary of Predictive Maintenance Benefits:
- Equipment Costs: Reduced costs by addressing issues early before they lead to expensive repairs or replacements.
- Labor Costs: Only necessary maintenance or parts replacement is carried out, cutting down on labor hours.
- Machine Uptime: Downtime becomes planned and scheduled, reducing the risk of unexpected machine failures.
- Safety: Predictive maintenance helps prevent accidents and creates a safer working environment by foreseeing issues before they become dangerous.
- Labor Time: Error detection and correction time is significantly reduced, leading to more efficient operations.
By integrating predictive maintenance, businesses can significantly enhance their operational efficiency, reduce costs, and ensure better uptime and safety within their production systems. This method of proactive maintenance is a crucial aspect of Industry 4.0, enabling smarter, more sustainable manufacturing practices.